Spring is planting season for Missouri farmer Jared Wilson. It’s his only opportunity during the year to get his corn and soybeans sown and sprayed. Not getting it right would affect his yield. But every year, he says, he struggles to get his John Deere equipment to do the job. Broken down combines, tractors and harvesters have cost him hundreds of thousands of dollars to fix.
“Time absolutely means money in this business,” Wilson said. “When you have machines that are failing at those critical times of the year — when you have that one shot to get things right — it can severely impact your bottom line.”
A U.S. Public Interest Research Group report published in 2023 estimated that farmers lose $3 billion to tractor downtime and pay $1.2 billion more in excess repair costs every year as a result of needing to rely on dealerships for repairs.
Wilson is among hundreds of farmers represented in class action lawsuits fighting for the “right to repair,” a movement that argues that customers should be able to fix their products when they break down or pay independent repair people to do so.
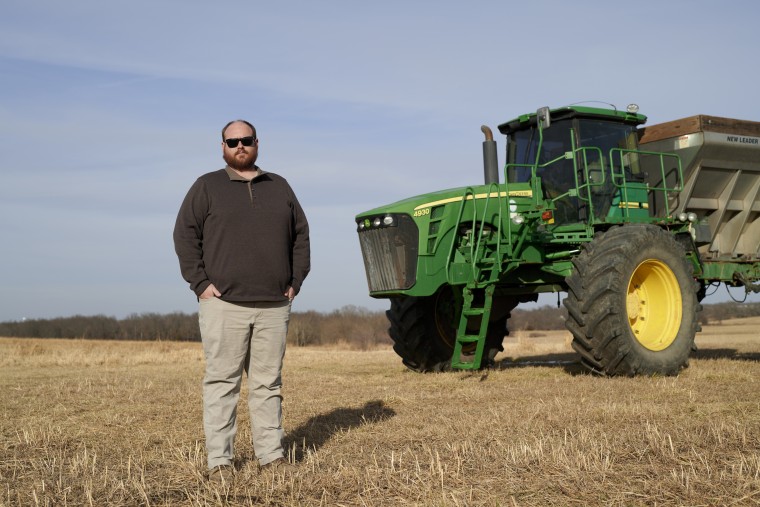
According to the lawsuit he is part of, Wilson and others accuse John Deere of blocking farmers and everyday mechanics from fixing equipment without going through John Deere dealers. Although the company doesn’t prohibit users from fixing equipment themselves, the lawsuit claims it locks users out of repairs because of the limited access to software that only dealerships can access. The lawsuit says that makes most fixes nearly impossible.A lot like cars, the farming equipment is equipped with sensors. The John Deere tractors, for instance, run on firmware that is necessary for basic functions, according to the lawsuit. If something is wrong with the equipment, a code will appear on a display monitor inside the machine. The suit says interpreting the error codes on tractors, for instance, requires software that “Deere refuses to make available to farmers.”
Right-to-repair advocates say the digitization of agricultural equipment — with its various computers and sensors — has made self-repair almost impossible, forcing farmers to depend on the manufacturers. Wilson, for example, said he has to rely on his local John Deere dealership, which he said takes longer and charges more than an independent repair worker.
In 2019, Wilson said, a John Deere dealership had his fertilizer spreader in the shop for 28 days before it was fixed. The dealership didn’t respond to a request for comment.
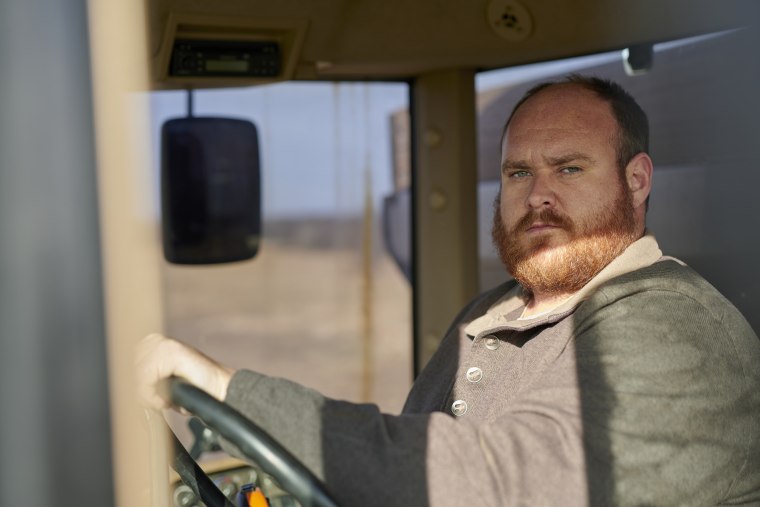
Wilson’s class action in U.S. District Court for Northern Illinois accuses John Deere of restricting access to the software needed for repairs, forcing farmers to rely on its authorized dealerships. The court denied John Deere’s attempt to dismiss the case, which is still pending.
This year, 20 states have introduced bills aimed at including agricultural equipment under right-to-repair laws. The bills fell through in Virginia and South Dakota.
Willie Cade has been traveling around the United States testifying on behalf of farmers since 2016. His grandfather Theo Brown was the chief engineer for John Deere in 1925 — long before the era of digitized farming equipment.
“Often the bills die in committee because the manufacturers have connections with one or two people who can influence the entire committee,” Cade said.
Farming equipment is exempted in five of the six states that have passed right-to-repair bills, including Minnesota, California and Massachusetts. That is due in part to a Memorandum of Understanding that John Deere signed with the American Farm Bureau in 2023 committing to providing “timely availability” of “tools, software and documentation” for repairs.
But a pending lawsuit the Federal Trade Commission filed Jan. 15 claims the company falls short of that promise. The complaint accuses it of unlawful business practices that have “inflated farmers’ repair costs and degraded farmers’ ability to obtain timely repairs.”
“I would have some farmers close to tears recalling the time they lost a whole harvest because they weren’t able to fix their own tractor and weren’t able to go to a local repair shop,” said former FTC Chair Lina Khan, who helped launch the suit.
John Deere denied nearly every allegation in the lawsuit. Its lawyers say that although the company has repair software that is available only to its dealerships, it also has a separate version for customers to use, which costs more than $3,000 per year. According to the company, the software can “conduct repairs while ensuring machine reliability, safety, and regulatory compliance.”
But Montana-based independent repair worker Brad Sage said the customer version of the software has some shortcomings. For example, he said, it won’t allow customers to repair the air conditioning on a tractor.
“You have to find a way to bootleg it and not do it legally above table,” Sage said of the customer software.
That’s exactly what he said he had to do to repair John Deere equipment. The software he relies on is a copy of the tool the company offers to its dealerships, but it’s purchased from an online third party.
Sage left his job at a John Deere dealership five years ago. Now, as an independent repair professional, he said, he charges farmers half the cost of a dealership and takes half the time for the same repairs.
John Deere told NBC News it plans to improve the repair software it offers to customers by early fall, allowing them to perform “limited calibrations” on their machinery. It wouldn’t comment on whether it intends to give them access to the full version of the software its authorized dealerships use.
The FTC maintains that the version available to customers is an inferior tool that is “not capable of enabling all repairs on Deere agricultural equipment.”
Time is running out for farmers
Cade thinks it could be five years before farmers are able to repair their own equipment, even if they win the FTC case.
Wilson, who started riding tractors when he was 4 years old, said he would rather give up the farm his family has run for a century than let Deere call the shots on when and how he can fix his own farm equipment.
“I have to be profitable to keep growing your food, or I’m not going to do it anymore,” Wilson said. “This is a problem that not only affects me, but it affects everyone in this country.”
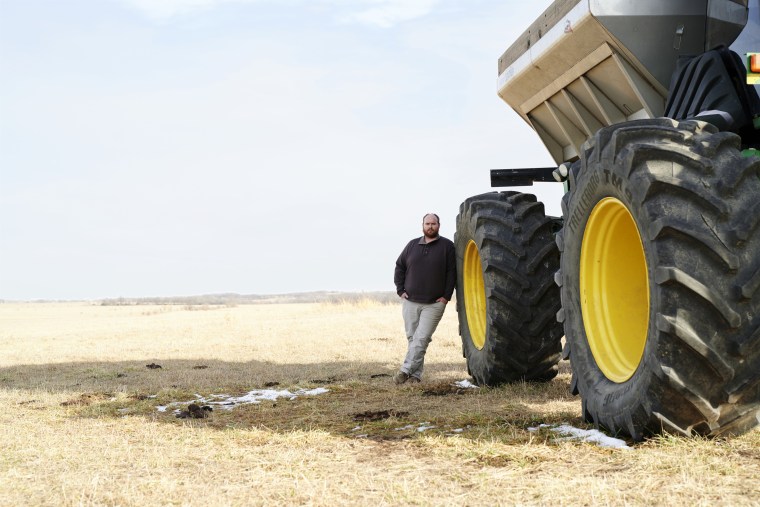